Ultrasonic-Cutting
Products
Ultrasonic-Cutting
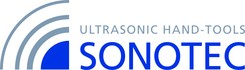
Features
- An ultrasonic cutter featuring the size convenient for carrying around
- The transducer is provided with a hand switch and the activation of operation is notified with illumination and sound
- The cutter can also be used as a versatile machine for cutting various materials.
This is a manual type ultrasonic cutter, which daringly pursued nice Features user-friendliness. It is provided with a portable handle and storage rack for use at various jobsites. It is best fitted for a wide range of applications including carbon prepregs, resins, rubber, and fabrics. For safety measures, the activation of ultrasonic vibration is reported with illumination and sound. The product complies with the CE Standard.
Applicable materials
- Carbon prepregs with thickness up to 10 mm
- Thermoplastics
- Rubber
- Fabrics
HP-2200
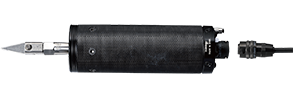
- Carbon prepreg
- Thermo plastics
- Cloth fabric
- Rubber 10t
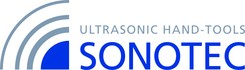
Feautures
- The output adjustment can be done in step-less and continuous manner from the minimum to the maximum levels.
- The SF-3400 II is a powerful ultrasonic oscillator that now also enables connection to PLC systems - ideal for modern Industry 4.0 environments.
- With digital signal output for load, amplitude and error types, the system offers a high level of transparency and process reliability in material processing.
This is a high-power ultrasonic cutter featuring the ultrasonic power output of 220 W. The tool’s ultrasonic vibrations at a frequency of 22 kHz(22,000 vibrations per second) drastically reduce the cutting resistance. Varieties of materials can be cut even more rapidly and cleanly with a lower processing pressure. A function to enable constant monitoring of loads during cutting was added anew, thereby ensuring added safety and user friendliness.
Applicable materials
- Plastics (boards, sheets, films, laminated materials)
- Various types of prepregs (single sheet cutting,overlapped cutting)
- Leather (natural and artificial)
- Rubber (vulcanized latex, non-vulcanized latex)
- Fabric materials, nonwoven fabrics
- Paper and cardboards
SF-3140

- Thermo plastics
- Prepreg
- Composite materials
- Rubber 10t
SF-7400
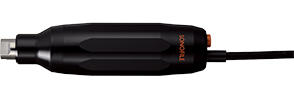
- Thermo Plastic
- Exterior walls
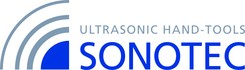
Feautures
- Powerful ultrasonic cutter with a maximum power output of 300 W
- Mountable on automated machinery, industrial robots and plotters
This ultrasonic oscillator is capable of exchanging signals with the main units of automated machinery, industrial robots, plotters, etc., for operations, such as turning on/off, emergency stop and switching the output level.
Applicable materials
- Various types of prepregs (boron, Kevlar, polyethylene fibers, etc.)
- Rubber (vulcanized latex, non-vulcanized latex, sheeting materials, sealing materials and tubes) and leather (natural and artificial)
- Thermoplastics (boards, sheeting materials, films, laminated materials, flooring materials)
- Fabric materials, nonwoven fabrics and paper (specially-treated paper and coated paper)
SF-8541RR
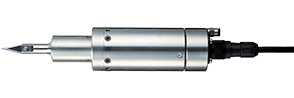
- Foamed materials
- Paper
- Composite materials
SF-8500RR
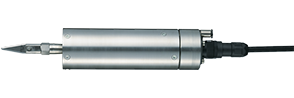
- Thermo plastics
- Prepreg
- Composite materials
- Rubber 10t
SF-3110
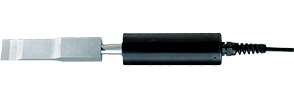
- Thermo plastics
- Rubber 10t
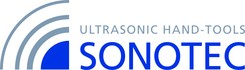
Features
- Cutter with a maximum power output of 500 W capable of handling materials requiring high-power cutting
- Tools including carbide blades and long blades can be used
- Mountable on automated machinery, industrial robots and plotters
The oscillator with a maximum power output of 500 W enabled powerful cutting of difficult-to-cut and extra-tough work pieces. Abrasion resistant carbide blade with 1 mm thickness can be used. Exchanging signals for on/off, emergency stop, change of output level, and other features with automated machinery or industrial robots is, of course, possible.
Applicable materials
- Carbon (CFRP)
- A range of prepregs (boron, kevlar, polyethylene fiber, etc,)
- Rubber (vulcanized latex, non-vulcanized latex, sheeting material, sealing material, tube)
- Thermoplastics (board, sheeting material, film and laminated material)
HP-2000
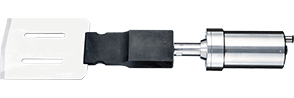
- Thermo plastic
- Prepreg
- Rubber 15t
HP-8701-C3
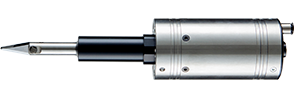
- Thermo plastic
- Carbon prepreg
- Composite materials
- Rubber 20t
SF-8500RR
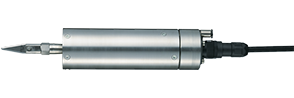
- Thermo plastics
- Prepreg
- Composite materials
- Rubber 10t
SF-3110
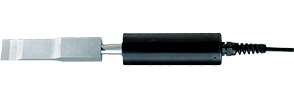
- Thermo plastics
- Rubber 10t
The ultrasonic cutter is composed of a “transducer” that generates vibration and an “oscillator” that drives the transducer. A piezoelectric element is used for the transducer. When voltage is applied, the piezoelectric element displaces the transducer by a few micrometers. Periodically applying voltage generates vibration. Each object has its special frequency, by which the object is stable and easy to vibrate. By adding an external force that corresponds to that special frequency, a small force can obtain a large vibration. This phenomenon is called resonance.
In the ultrasonic cutter, the piezoelectric element generates a force that resonates the whole body, from the transducer to the blade tip, generating a large vibration at the tip. The oscillator periodically generates voltage to resonate and drive the transducer. Using a component of the ultrasonic cutter called the horn to wring the cross-sectional area, from the piezoelectric element to the blade tip, can obtain a larger vibration